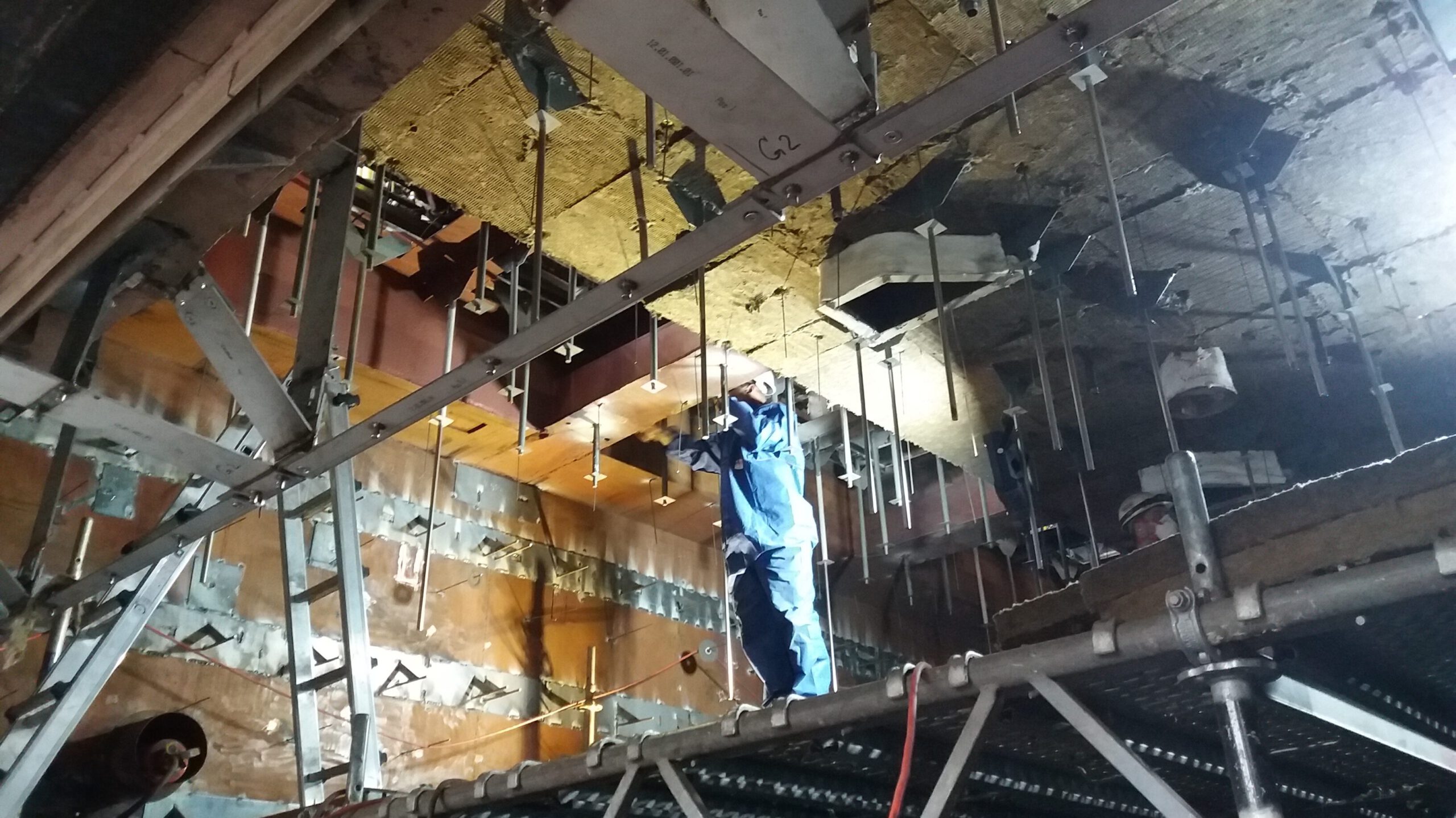
Zusammen mit unseren Partnern Reimann und Stadler Industries wurde bei der Alvance Aluminium Duffel BV (vormals Aleris Aluminium Duffel BVBA) ein Stoßofen saniert. Ziel war die nachhaltige Reduzierung der Energiekosten durch eine verbesserte Dämmung, sowie die Erhöhung der Prozesssicherheit und des Durchsatzes durch ein integriertes Prozessmodell und die weitere Optimierung der Steuerungsprozesse. Dieser Beitrag konzentriert sich auf das von der Prosik gelieferte integrierte Prozessmodell. Details zur Sanierung des Ofens wurden in [1] veröffentlicht.
Optimierung der Prozessführung
Die Verbesserung der Prozessführung war neben den konstruktiven Änderungen an der Anlage ein wichtiger Aspekt des Projektes. Bisher wurde ohne Überziehtemperatur gefahren. Das heißt, die Temperatur der Ofenatmosphäre entspricht der Solltemperatur der Barren. Daher wird die Differenz zwischen Atmosphären- und Barrentemperatur während des Aufheizens immer geringer. Das wiederum hat sehr lange Aufheizzeiten zur Folge, was den Durchsatz des Ofens begrenzt. Da jedoch die aktuelle Barrentemperatur bei laufender Produktion vor der Modernisierung nicht bekannt war, musste dieser Nachteil im Hinblick auf die Prozesssicherheit in Kauf genommen werden.
Im Zuge der Modernisierung wurde der Ofen in jeder Zone mit Andrückthermoelementen ausgestattet, die eine Temperaturmessung im laufenden Betrieb ermöglichen. Aufgrund der Konstruktion des Ofens sind die Thermoelemente durch die Decke geführt worden. Dementsprechend wird die Oberflächentemperatur an der oberen Kante des Barrens gemessen. Allerdings strömt die heiße Luft im Ofen auf der Unterseite ein und wird oben wieder angesaugt. Daher ist die höchste Temperatur beim Aufheizen an der Unterseite des Barrens zu erwarten.
Da diese Position messtechnisch nicht zugänglich ist, wird die Temperatur dort mit Hilfe eines integrierten Prozessmodells fortlaufend berechnet. Dies erlaubt eine Abschätzung des Temperaturprofils des Barrens, insbesondere eine Aussage über die minimale und maximale Temperatur. Mit diesen Informationen kann die Umschaltung von der Aufheiz- in die Haltephase optimal bestimmt und die Überziehtemperatur sicher eingestellt werden. Diese beiden Faktoren führen zu einer Verkürzung der Durchlaufzeit und damit zu einer Steigerung der Produktivität der Anlage.
Das integrierte Prozessmodell
Eine Anforderung an das Modell war, dass es direkt auf der SPS laufen soll. Daher muss die Berechnung der Barrentemperatur an der Unterseite für jede Zone mit relativ geringen Ressourcen möglich sein. Um das zu erreichen, wurden daher zunächst umfangreiche FVM-Simulationen des Prozesses durchgeführt, um die Einflüsse der verschiedenen Prozessparameter zu ermitteln. So wurden verschiedene Barrengeometrien und Legierungen untersucht, sowie die Prozessparameter des Ofens wie die Temperatur und die Drehzahl der Umwälzventilatoren.
Mit den Daten aus den FVM-Simulationen wurde ein vereinfachtes Modell erstellt, das den Prozess als ein Verzögerungsglied erster Ordnung nach (1) abbildet. Dabei ist der Wert der Sprungantwort zum Zeitpunkt , der dem Signal verzögert folgt. Durch die Zeitkonstante wird die Trägheit des Systems beschrieben. Aufgrund der Form von (1) ist gegeben, dass nach einer Dauer von erfüllt ist. Abbildung 2 zeigt die Lösung von (1) für einen konstanten Wert und einen zeitlich variablen Wert . Im letzteren Fall ist die Ähnlichkeit zu einem Aufheizprozess in einem Stoßofen zu erkennen.
f^{n+1} = f^n + \left( K^{n+1} - f^n \right) \left(1 - e ^{-\frac{\Delta t}{\tau}} \right) \qquad \qquad (1)
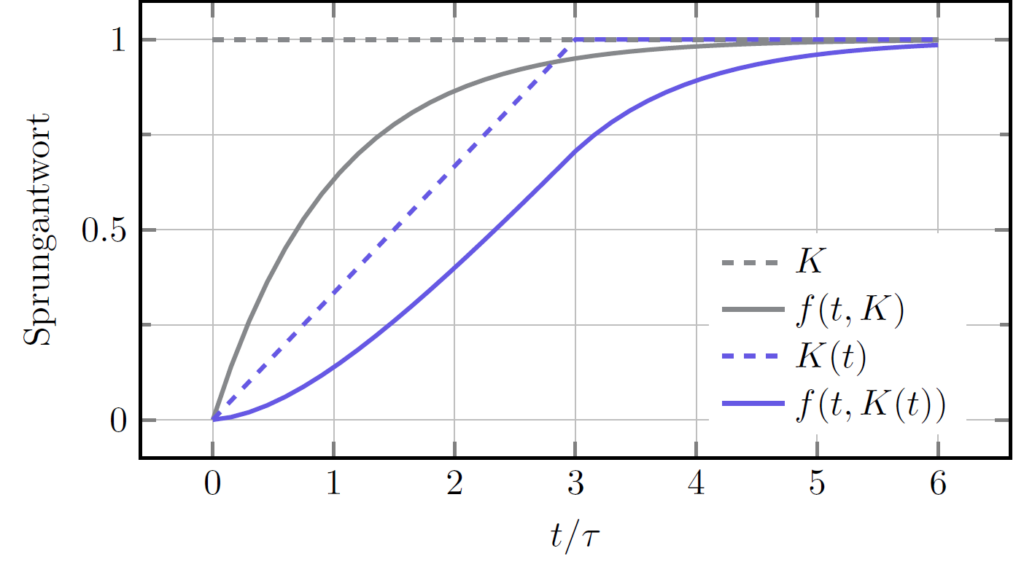
Mit Hilfe der Daten aus den FVM-Simulationen wurde die Zeitkonstante \tau
in Abhängigkeit der Barrengeometrie, der Dichte, der Wärmeleitfähigkeit, der spezifischen Wärmekapazität, der Ofentemperatur und der Ventilatordrehzahl bestimmt. Durch eine Kombination zweier Verzögerungsglieder konnte eine gute Übereinstimmung des Modells mit gemessenen Daten erzielt werden. Dementsprechend gibt es eine Zeitkonstante \tau_L
, die sich auf die Lufttemperatur des Ofens T_L
bezieht und eine Konstante \tau_O
, die sich auf die gemessene Barrentemperatur an der Oberseite T_O
bezieht. Die Temperatur an der Unterseite T_U
wird nach (2) bestimmt.
T^n_U = T^{n-1}_U + \left( T^n_L - T^{n-1}_U \right) \left(1-e^{-\frac{\Delta t}{\tau_L}} \right) + \left( T^n_O - T^{n-1}_U \right) \left( 1 - e^{-\frac{\Delta t}{\tau_O}} \right) \qquad (2)
Bewertung des Modells
Zur Bewertung des Modells wird ein mit eingebohrten Thermoelementen präparierter Messbarren in den Produktionsprozess eingeschleust. Der Verlauf der wichtigsten Prozessparameter für eine solche Messung ist exemplarisch in Abbildung 3 dargestellt. Zu Beginn der Messung ist der Ofen in der Aufheizphase, sodass die Atmosphärentemperatur T_L
zunächst noch ansteigt. Die Barrentemperatur an der Oberseite T_O
wird durch die beschriebenen Andrückthermoelemente gemessen. Aufgrund der eingebohrten Thermoelemente liegt ein Messwert für die Temperatur an der Unterseite des Barrens T_{U, \text{mess}}
vor. Dieser wird durch \Delta T_\text{mod} = T_{U, \text{mod}} - T_{U, \text{mess}}
mit der modellierten Temperatur T_{U, \text{mod}}
verglichen.
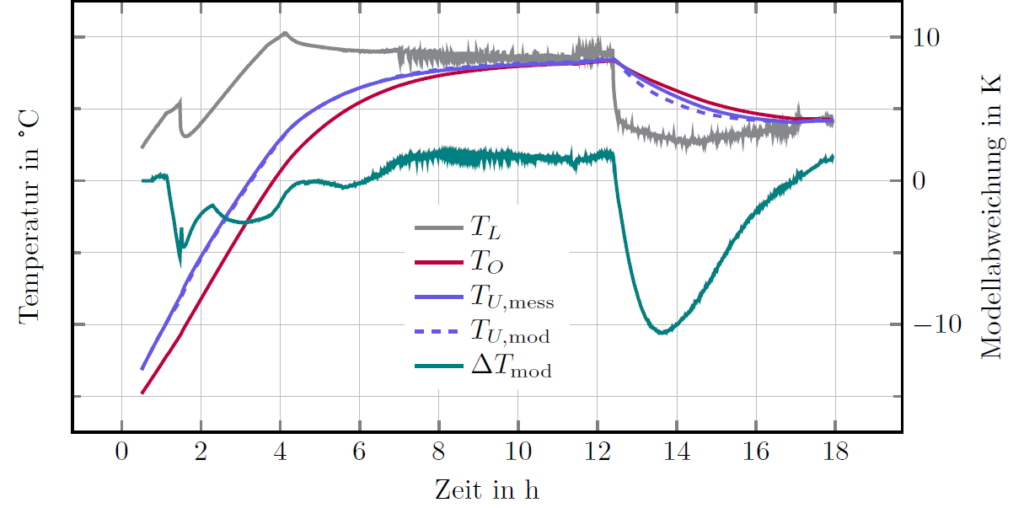
Aus der Abbildung ist zu erkennen, dass der modellierte Temperaturverlauf gut mit dem gemessenen übereinstimmt. Lediglich zu Beginn des Kühlvorgangs kommt es zu Abweichungen in der Größenordnung von 10 Kelvin. Dies ist jedoch im Hinblick auf die Steuerung der Überziehtemperatur zu verkraften. Daher ist das Modell geeignet, die Temperatur an der Unterseite des Barrens zu berechnen. Die Anforderung, dass das Modell mit den Rechenkapazitäten der SPS betrieben werden kann wird ebenfalls erfüllt. Nun kann der Prozess sowohl beim Heizen als auch beim Kühlen mit größeren Überziehtemperaturen als vorher gefahren werden. Dies hat eine Verkürzung dieser Prozessschritte und damit eine direkte Erhöhung des Durchsatzes zur Folge.
Literatur
[1] Schmitt, A.: Sanierung und Prozessoptimierung eines Barrenstoßofens. In:
Aluminium Praxis 26 (2021), Nr. 1, S. 23–25