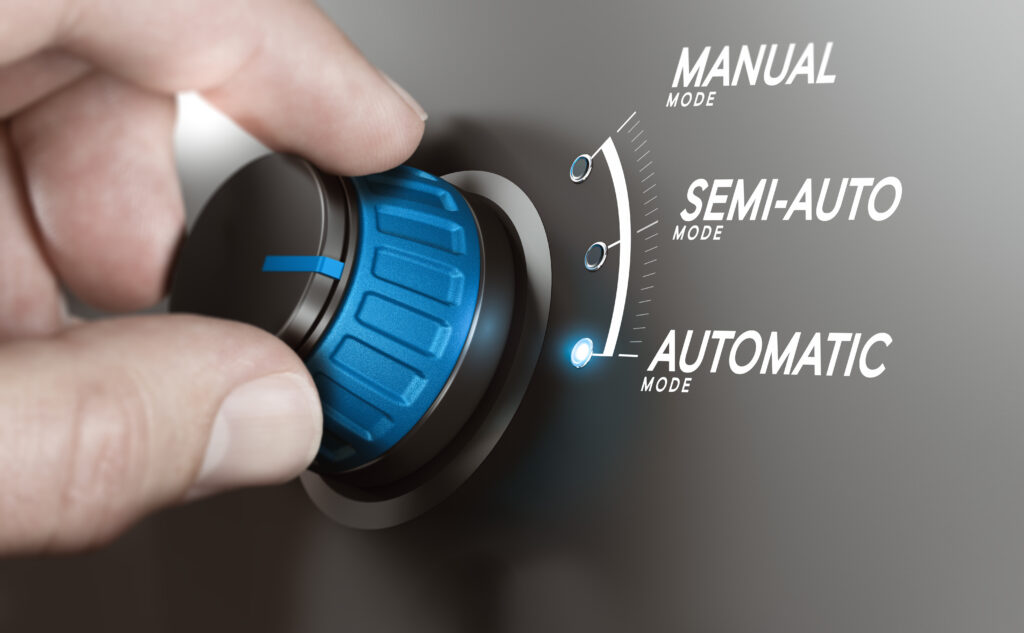
Ein integriertes Prozessmodell zeichnet sich durch die direkte Einbettung in die Steuerungslandschaft einer Industrieanlage aus. Durch die Simulation des Prozesses in Echtzeit stehen wichtige Informationen wie die Temperaturverteilung innerhalb des Materials für die Regelung des Prozesses zur Verfügung. Dies ermöglicht die nächste Stufe der Automatisierung, bei der der Prozess dynamisch gefahren und unmittelbar anhand der metallurgisch relevanten Größen (Haltezeit, Temperatur, Abkühlrate) bewertet wird.
Was ist ein integriertes Prozessmodell?
Mit Hilfe von Großrechnern können heute mittels FEM, FVM und CFD auch sehr komplexe instationäre Prozesse mit kompressiblen Strömungen wie beispielsweise die Sauerstoffinjektion in die Schmelze innerhalb eines Elektrolichtbogenofens [OKKV19] detailliert abgebildet werden. Mit modernen Rechenclustern lassen sich bis zu einige hundert Millionen Gitterzellen noch gut umsetzen. Modelle dieser Art zielen darauf ab, den Prozess hinsichtlich einer konkreten Fragestellung genau abzubilden und zu optimieren. Sie erfordern Rechenzeiten von mehreren Stunden oder Tagen und werden daher im Rahmen der Auslegung oder der Optimierung von Anlagen abseits des eigentlichen Prozesses eingesetzt.
Im Gegensatz dazu gibt es Modelle, die direkt in die Steuerungslandschaft eines Industrieofens integriert sind [vK21] und den laufenden Prozess parallel in Echtzeit abbilden. Diese Modelle müssen in der Regel mit weniger Ressourcen auskommen und werden entweder direkt in der SPS oder auf einem mit der SPS verbundenen Industrie-PC betrieben. Abbildung 2 zeigt die Kommunikationswege bei der Verwendung eines integrierten Prozessmodells. Die SPS liest kontinuierlich die Daten der Sensoren der Anlage aus, verarbeitet sie und leitet sie an die Bedienerschnittstelle und das Prozessmodell weiter. Das Prozessmodell simuliert den Prozess anhand der Ist-Werte aus der SPS und gibt die Ergebnisse an die SPS und die Schnittstelle weiter. Über die Schnittstelle kann der Bediener die Daten einsehen und Eingaben vornehmen.
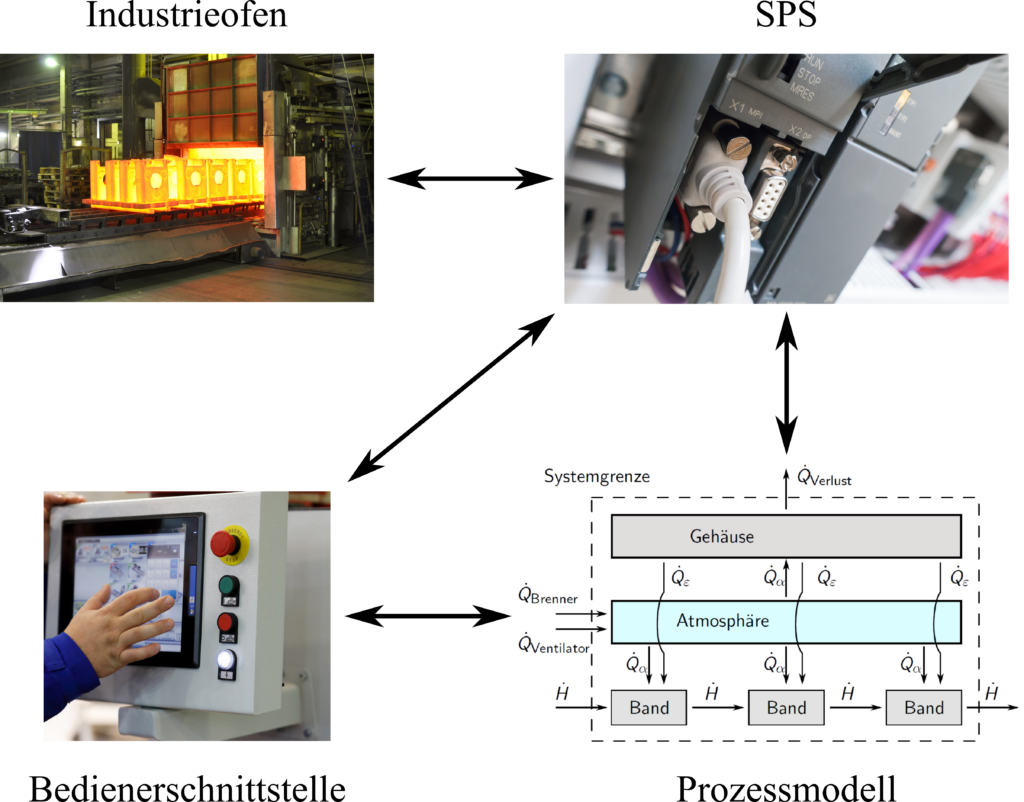
Vorteile eines integrierten Prozessmodells
Durch den Einsatz eines integrierten Prozessmodells ergeben sich für den Anlagenbetreiber eine Reihe von Vorteilen. Durch die kontinuierliche Simulation anhand der Ist-Daten aus der SPS entsteht durch das Modell ein digitaler Zwilling des zu erwärmenden Werkstücks. Das bedeutet, dass die Temperaturverteilung im Material T(x,y,z,t) sowohl räumlich als auch zeitlich bestimmt und für die Regelung des Prozesses verwendet werden kann. Statt auf indirekte Größen wie beispielsweise die Ofenraumtemperatur zu schauen, kann der Prozess direkt anhand der eigentlich metallurgisch relevanten Größen wie Temperatur, Haltezeit oder Abkühlrate des Materials geregelt werden.
Dies ermöglicht eine dynamische Fahrweise des Prozesses, bei der nur das Ergenbis der Wärmebehandlung (Materialtemperatur) vorgegeben wird, nicht aber der Weg dorthin (Ofentemperatur). Dieser Ansatz stellt eine neue Stufe der Automatisierung dar, denn die Steuerung kann nun flexibel auf Störungen reagieren. Fällt beispielsweise ein Brenner in einem Durchlaufofen aus, so wird automatisch die Temperatur in den benachbarten Zonen nach oben korrigiert, um die vorgegebene Materialtemperatur trotzdem zu erreichen. Die Anlage kann weiter produzieren, bis der Fehler zu einem geeigneten Zeitpunkt behoben wird. An einem Ofen zur Wärmebehandlung von Stahl wurde mit diesem Ansatz eine Steigerung der Produktivität von bis zu 10 % erreicht [WEB20].
Neben der Erhöhung der Flexibilität kann ein integriertes Prozessmodell auch genutzt werden um aufwändige Temperaturmessungen zu ersetzen. Dies zeigt das Beispiel der induktiven Bolzenerwärmung. Dort wird die berechnete Temperatur des Modells anstatt der durch spezielle Andrückthermoelemente gemessene Temperatur als Regelgröße verwendet. Dies führt zu einer Verbesserung der Temperaturgleichmäßigkeit und der Wiederholgenauigkeit des Prozessses. Außerdem können die wartungsintensiven Thermoelemente mittelfristig wegfallen.
Prozessmodelle für bestehende und neue Anlagen
Integrierte Prozessmodelle sind die moderne Art der Anlagensteuerung. Sie lassen sich dennoch problemlos auch für bestehende Anlagen umsetzen. Die Sensorik einer bestehenden Anlage ist oft ausreichend, sodass ohne großen Aufwand ein Modell umgesetzt und die Produktivität der Anlage gesteigert werden kann. Bei neuen Anlagen können die Möglichkeiten integrierter Prozessmodell bereits in der Planungsphase berücksichtigt werden. Sprechen Sie uns einfach an.
Literatur
[OKKV19] | Odenthal, H.J. ; Kemminger, A. ; Krause, F. ; Vogl, N.: Strömungssimulation in der metallurgischen Verfahrenstechnik – Möglichkeiten und Grenzen. In: Pfeifer, H. (Hrsg.) ; Echterhof, T. (Hrsg.): 2. Aachener Ofenbau- und Thermoprozess-Kolloquium. Bottrop: Blinn & Reichel Market-Ing, 2019, S. 45 -59 |
[vK21] | van Treek, J. ; Künne, S.: Integriertes Prozessmodell für die induktive Bolzenerwärmung. In: Int. Aluminium Journal 97 (2021), Nr. 3, S. 43-48 |
[WEB20] | Wuppermann, C. ; Eggert, W. ; Berghof, K.: Inline-Prozessmodell: Produktivitäts- und Qualitätssteigerung in der kontinuierlichen Wärmebehandlung von Stahlband. In: Prozesswärme 3 (2020), Nr. 1, S. 43-49 |