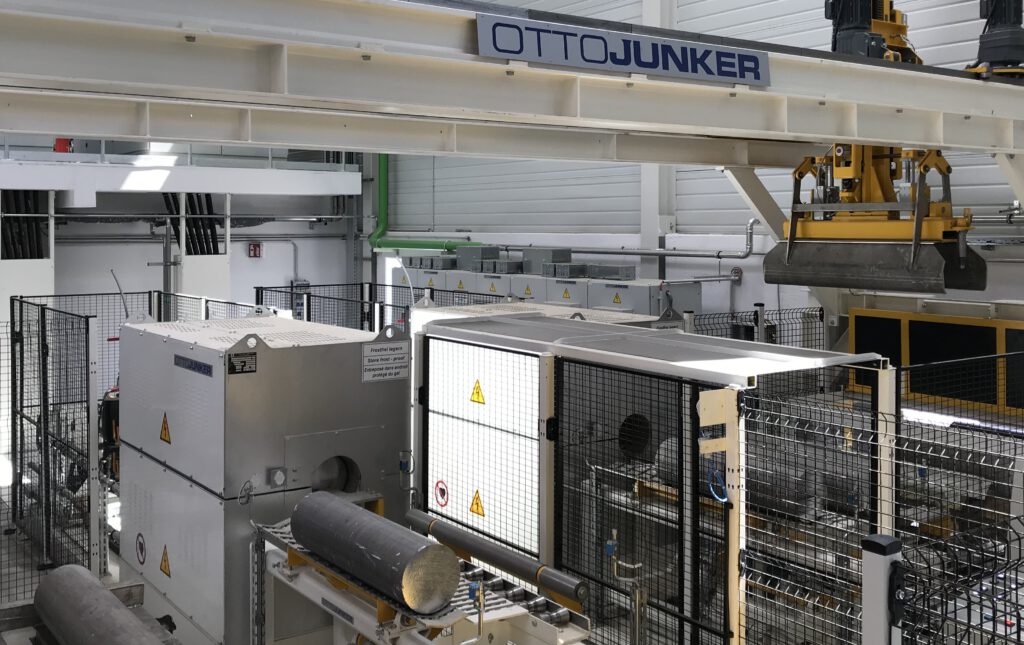
Zur Prozesssteuerung von Anlagen zur induktiven Bolzenerwärmung werden Andrückthermoelemente verwendet. Anhand der so gemessenen Oberflächentemperatur an mehreren Positionen wird die elektrisch induzierte Leistung geregelt. Die Thermoelemente sind jedoch ungenau und wartungsintensiv. Außerdem fehlen Informationen bezüglich der radialen Temperaturverteilung. Daraus resultiert eine schlechte Wiederholgenauigkeit des Prozesses, was die Betreiber von Strangpressanlagen immer wieder vor Probleme stellt.
Die Prosik GmbH hat zusammen mit der Otto Junker GmbH und der Constellium Singen GmbH ein integriertes Prozessmodell entwickelt und erfolgreich in Betrieb genommen. Anhand der Leistungsaufnahme der Induktionsspulen berechnet das Modell die Verteilung der Leistungsdichte im Bolzen. Anschließend wird daraus mit Hilfe eines FVM-Modells die räumliche und zeitliche Temperaturverteilung ermittelt. Mit diesen Informationen ist die optimale Regelung der elektrischen Leistung möglich. Mit diesem Vorgehen wird die Wiederholgenauigkeit und die Stabilität des Prozesses verbessert.
Induktive Bolzenerwärmung
Zur Herstellung von Strangpressprofilen werden gegossene Aluminiumbolzen unter hohem Druck durch eine Matrix gepresst. Ein Anwärmen der Bolzen vor dem Pressen minimiert die dazu erforderlichen Kräfte. Aufgrund der auftretenden Umformwärme erhöht sich die Temperatur an der Matrix im Laufe des Prozesses. Für ein möglichst gleichmäßiges Pressergebnis ist jedoch eine konstante Temperatur von Vorteil. Daher werden die Bolzen so erwärmt, dass sich ein Temperaturgefälle entlang der Längsachse einstellt, der sogenannte Taper. Die induktive Bolzenerwärmung ist in diesem Zusammenhang eine bewährte Technik.
Abbildung 1 zeigt die Pilotanlage, für die das Modell entwickelt worden ist. Der Bolzen wird auf einer Transportschale abgelegt und anschließend in den Ofen gefahren. In diesem Fall existieren sechs unabhängig voneinander ansteuerbare Teilspulen. Diese sind so konstruiert, dass speziell gefertigte Thermoelemente durch einen Kanal auf die Oberfläche des Bolzens gedrückt werden können. Die Anlage wird zur Erwärmung von Bolzen aus verschiedenen Aluminiumlegierungen mit einem Durchmesser von 254 mm und einer maximalen Länge von 1500 mm genutzt. Diese können innerhalb von circa 150 s auf bis zu 550 °C erwärmt werden.
Der Bolzen verbleibt nach dem Erwärmen bis zum Abruf durch die Presse im Ofen und wird auf Temperatur gehalten. Bei Abruf des Bolzens wird dieser auf der Tragschale aus dem Ofen gefahren, vom Manipulator aufgenommen und zu einer Messstation befördert. Auch hier wird mit pneumatisch betriebenen Andrückthermoelementen die Temperatur des Bolzen erfasst. Liegt diese innerhalb der vorgeschriebenen Toleranz, wird der Bolzen zum Pressen freigegeben. Andernfalls wird er aussortiert und entweder verschrottet oder zu einem späteren Zeitpunkt erneut erwärmt.
Schwachstellen der konventionellen Fahrweise
Abbildung 2 zeigt den Verlauf der elektrischen Leistungsaufnahme, der gemessenen Temperatur und des Sollwerts für eine Teilspule bei konventioneller Fahrweise. Nach dem ersten Erreichen des Sollwertes nach etwa 100 s wird die elektrische Leistung reduziert und der im Rezept festgelegte Überziehwert einmalig angefahren. Aufgrund des Skin-Effektes [1] wird über 90 % der Leistung in den äußeren 20 mm des Bolzens induziert. Der entstehende radiale Temperaturgradient wird durch Wärmeleitung mit der Zeit ausgeglichen. Dies führt anfangs bei ausgeschalteter Spule zu einem starken Abfall der Oberflächentemperatur. Diese wird nun mit Hilfe eines Zweipunktreglers nahe der Solltemperatur gehalten. Der zeitliche Abstand zweier Heizvorgänge wird als Indikator dafür verwendet, wann der Bolzen gleichmäßig durchwärmt und damit abrufbereit ist. Diese Regelung führt selbst bei einer idealen Temperaturmessung je nach Entnahmezeitpunkt des Bolzens zu einer Gleichmäßigkeit von bestenfalls +- 5 K.
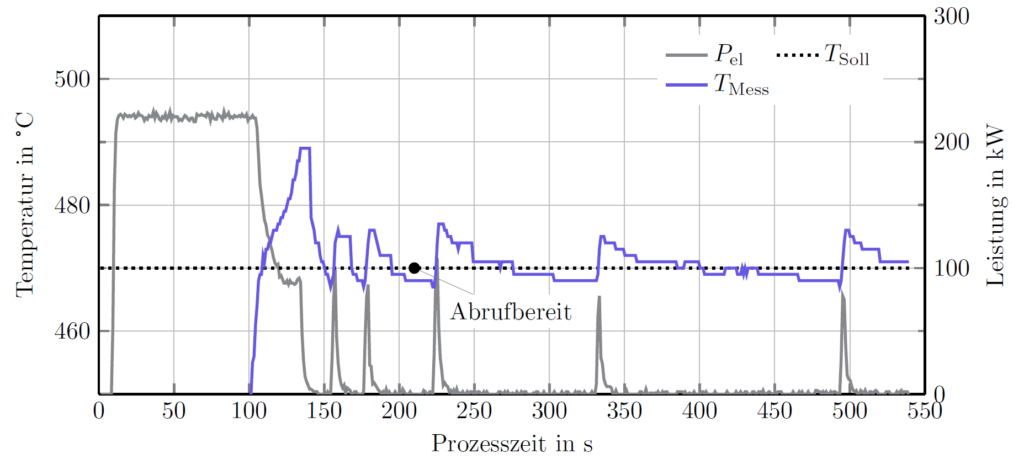
Die gemessene Temperatur ist jedoch nicht ideal, sondern fehlerbehaftet. Die Bolzen weisen teilweise sehr unterschiedliche Oberflächenbeschaffenheiten auf. Das Spektrum reicht von einer blanken Oberfläche bis hin zu Bolzen mit einer ausgeprägten Gusshaut. Um die Gusshaut zu durchdringen, müssen die Thermoelemente mit hoher Kraft auf die Oberfläche gedrückt werden. Durch die Verwendung von Elementen mit einem Schenkeldurchmesser von 8 mm wird die erforderliche mechanische Belastbarkeit erreicht. Dennoch ist die Kontaktierung aufgrund der unterschiedlichen Bolzenoberflächen und teilweise mangelnder Wartung ungleichmäßig. Dies wirkt sich zusammen mit dem hohen Wärmeabfluss durch die Thermoelemente negativ auf die Qualität der Messung aus [2]. Daher sind in der Praxis teilweise deutlich höhere Temperaturtoleranzen zu beobachten. Die Thermoelemente müssen regelmäßig ausgebaut und angeschliffen werden. Außerdem neigen sie zu einem starken Driftverhalten.
Entwicklung des integrierten Prozessmodells
Die Prosik GmbH hat zusammen mit der Otto Junker GmbH und der Constellium Singen GmbH ein integriertes Prozessmodell entwickelt, das die angeführten Schwachstellen beseitigt. Ein integriertes Prozessmodell läuft entweder auf der SPS der Anlage oder auf einem Industrie-PC, der direkt mit der SPS und dem MMI kommuniziert. Es ist in der Lage, den Prozess in Echtzeit zu simulieren, sodass die Ergebnisse der Simulation zur Steuerung des selben genutzt werden können. Die Simulation der induktiven Erwärmung eines Bolzens mit Hilfe der Finite Elemente Methode ist Stand der Technik [3]. Aufgrund der hohen erforderlichen Rechenleistung ist eine direkte Nutzung von FEM-Simulationen im Sinne eines integrierten Prozessmodells jedoch nicht sinnvoll möglich.
Daher wurde im ersten Schritt ein empirisches Modell für die Verteilung der Leistungsdichte im Bolzen entwickelt. Dieses basiert auf zuvor durchgeführten FEM-Simulationen, bei denen die unterschiedlichen Betriebszustände der Anlage untersucht worden sind. Dies schließt insbesondere verschiedene Kombinationen von aktiven und ausgeschalteten Spulen, sowie unterschiedlich lange Bolzen ein. Die Einbettung des Prozessmodells in die Steuerungslandschaft ist in Abbildung 3 dargestellt. Anhand der Leistungsaufnahme der Spulen wird mit dem vereinfachten Modell die Verteilung der Leistungsdichte ermittelt und an ein FVM-Modell übergeben.
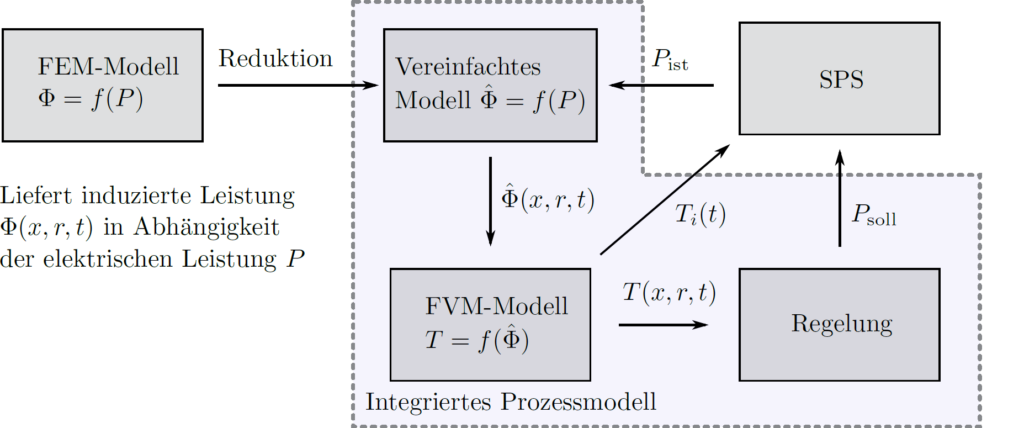
Dieses berechnet daraus unter Berücksichtigung der Wärmeleitung und der Oberflächenverluste die Temperaturverteilung im Bolzen. Ein Schalenelement des Bolzens ist in Abbildung 4 dargestellt. Die induzierte Leistung wird als Quellterm berücksichtigt. Weiterhin werden die Wärmeströme aufgrund von Wärmeleitung entlang der Längsachse, des Radius und des Umfangs abgebildet. Die aus der freien Konvektion an der Oberfläche auftretenden Verluste werden ebefalls simuliert.
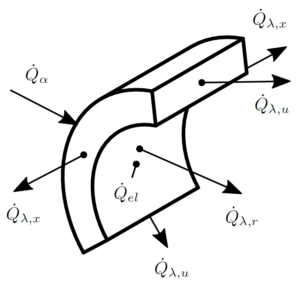
Steuerung des Prozesses durch das Modell
Die mit Hilfe des FVM-Modells berechnete örtliche und zeitliche Temperaturverteilung wird an die Regelung übergeben. Die berechnet daraus die Sollwerte für die elektrische Leistungsaufnahme der Spulen. Der resultierende Prozessverlauf ist in Abbildung 5 dargestellt. Zunächst wird die Oberflächentemperatur auf den erlaubten Überziehwert geregelt. Dabei wird kontinuierlich auch die mittlere Temperatur, die aufgrund der Simulation nun bekannt ist, betrachtet. Nähert sich diese dem Sollwert an, wird die Regelung umgeschaltet, sodass die mittlere Temperatur auf den Sollwert geregelt wird.
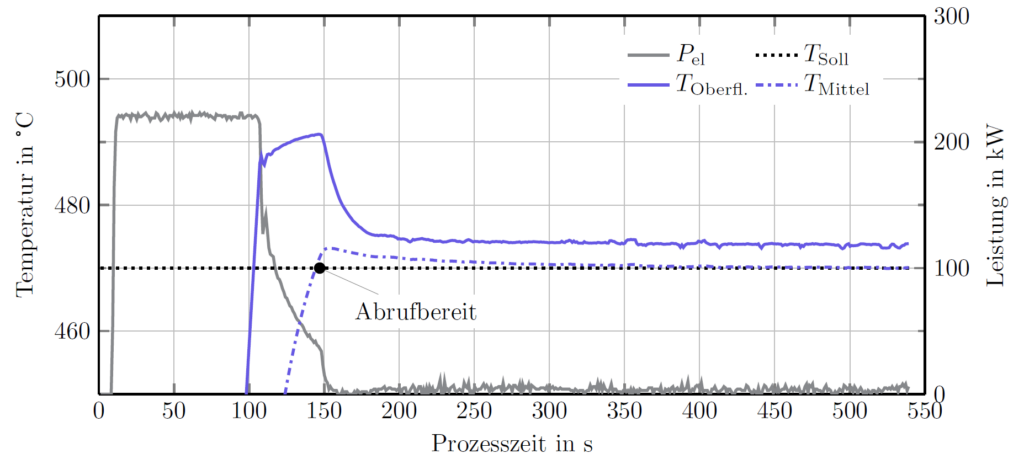
Im Vergleich zum konventionellen Prozess aus Abbildung 2 zeigt sich, dass die Temperaturgleichmäßigkeit aufgrund der gleichmäßigeren Beheizung besser ist. In der Abbildung wird die erste Teilspule betrachtet, bei der die Verluste wegen der Stirnfläche des Bolzens besonders hoch sind. Daher liegt die Oberflächentemperatur hier über dem Sollwert. Diese Tatsache wird bei der konventionellen Fahrweise nicht berücksichtigt.
Durch die Kenntnis der mittleren Temperatur kann besser beurteilt werden, wann der Bolzen abrufbereit ist. Durch den modernen Regelungsansatz kann auch die Überziehtemperatur besser ausgenutzt und somit der Durchsatz leicht gesteigert werden. Ist die anfängliche Temperatur des Bolzen bekannt, kommt das Modell im Prozess ohne die wartungsintensiven Thermoelemente aus. Dies ist insbesondere in der letzten belegten Spule nützlich, wenn der Bolzen nicht lang genug ist, um von den Andrückelementen erreicht zu werden.
Gute Übereinstimmung mit den Messwerten
Zur Validierung des Modells wird ein spezieller Messbolzen verwendet. Dieser ist mit insgesamt 13 Mantelthermoelementen bestückt, die durch Bohrungen in unterschiedlichen Tiefen angebracht sind. Für jede Spule wird die Kerntemperatur des Bolzens, sowie die Temperatur im Abstand von 25 mm zur Oberfläche gemessen. Das dreizehnte Element befindet sich im Kern des Bolzens mit einem Abstand von 25 mm zur Stirnseite. Abbildung 6 zeigt exemplarisch die Auswertung für eine Teilspule. Die Indizes 0, 25 und K stehen für die Messung an der Oberfläche, in 25 mm Abstand zur Oberfläche beziehungsweise im Kern. Kurven mit dem Index TC sind entweder durch die Andrückelemente oder durch die eingebohrten Thermoelemente gemessen. Die durchgezogenen Kurven mit dem Index M stehen für die an der entsprechenden Stelle modellierten Temperaturen. Diese stimmen gut mit den gemessenen Temperaturen überein. Insbesondere im ausgeglichenen Zustand ab 120 s sind die Abweichungen minimal.
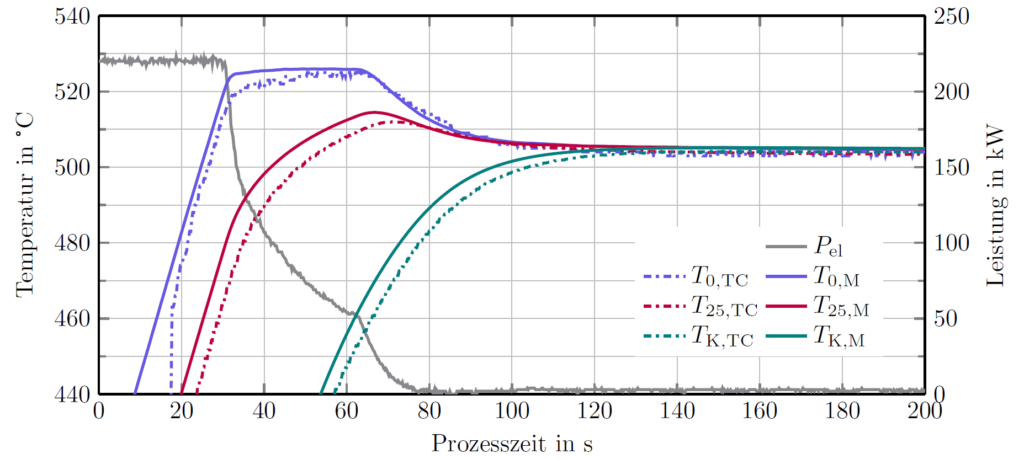
Verbesserung der Temperaturgleichmäßigkeit
Mit der Entwicklung des integrierten Prozessmodells wurde das Ziel verfolgt, die Temperaturgleichmäßigkeit des Prozesses zu verbessern. In Abbildung 7 sind die an der Messstation gemessenen Werte für den Betrieb mit Modell und die konventionelle Fahrweise dargestellt. Durch die Verwendung des integrierten Prozessmodells hat sich die Reproduzierbarkeit verbessert. Insbesondere spielen beim Betrieb mit Modell die äußeren Randbedingungen wie die Oberfläche des Bolzens oder der Zustand der Thermoelemente keine große Rolle. Die verbesserte Gleichmäßigkeit wird dauerhaft erreicht. Darüber hinaus wird ein stabilerer Prozessablauf erzielt, da im herkömmlichen Betrieb fehlerhafte Temperaturmessungen Störungen in der Anlage verursachen können.
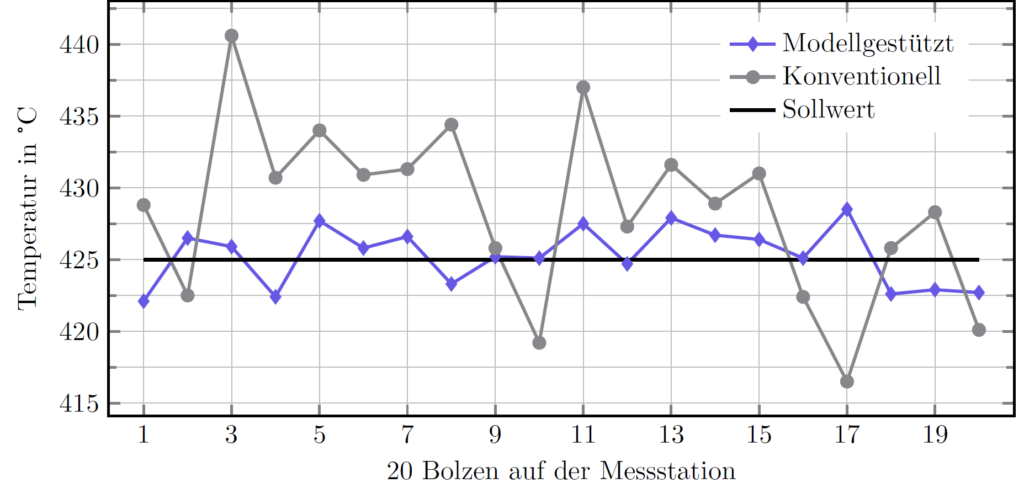
Mittelfristig sollen die Andrückthermoelemente wegfallen und durch eine weniger aufwändige Methode zur Bestimmung der Anfangstemperatur des Bolzens ersetzt werden. Dies reduziert den Wartungsaufwand und die Betriebskosten der Anlage. Der Prozess wird Stand heute schon „blind“ betrieben. Da die Andrückelemente an der Pilotanlage bereits vorhanden waren, werden sie als zusätzliche Sicherheit noch zur Überwachung genutzt.
Zusammenfassung
Durch den Einsatz des integrierten Prozessmodells werden mehrere Aspekte verbessert. Durch die Reduktion der Ausgleichszeit wird ein höherer Durchsatz erreicht. Die Prozesssicherheit steigt aufgrund zuverlässigerer Temperaturdaten. Anhand dieser Daten können durch die neue Regelstrategie langfristig enge Temperaturtoleranzen auch unter ungünstigen Bedingungen garantiert werden. Gleichzeitig sinkt der Wartungsaufwand durch die bisher verwendeten Thermoelemente.
Bisher wurden nur die Auswirkungen auf die reine Erwärmung des Bolzens untersucht. Speziell das Zusammenwirken mit der Strangpresse, die nun noch homogeneres Einsatzgut zur Verfügung gestellt bekommt und damit am optimalen Betriebspunkt arbeiten kann, wurde noch nicht betrachtet. Auch in diesem Zusammenhang sind weitere Verbesserungen des Gesamtprozesses und damit am Produkt zu erwarten.
Literatur
[1] Jackson, J.D.:Classical Electrodynamics, 2nd Edition. Wiley 1975.
[2] Körtvélyessy, D. und Körtvélyessy, L.: Thermoelement Praxis, 4. Auflage. Vulkan-Verlag GmbH, 2015.
[3] Aschendorf, B.: FEM bei elektrischen Antrieben 1. Vieweg + Teubner Verlag, 2014.
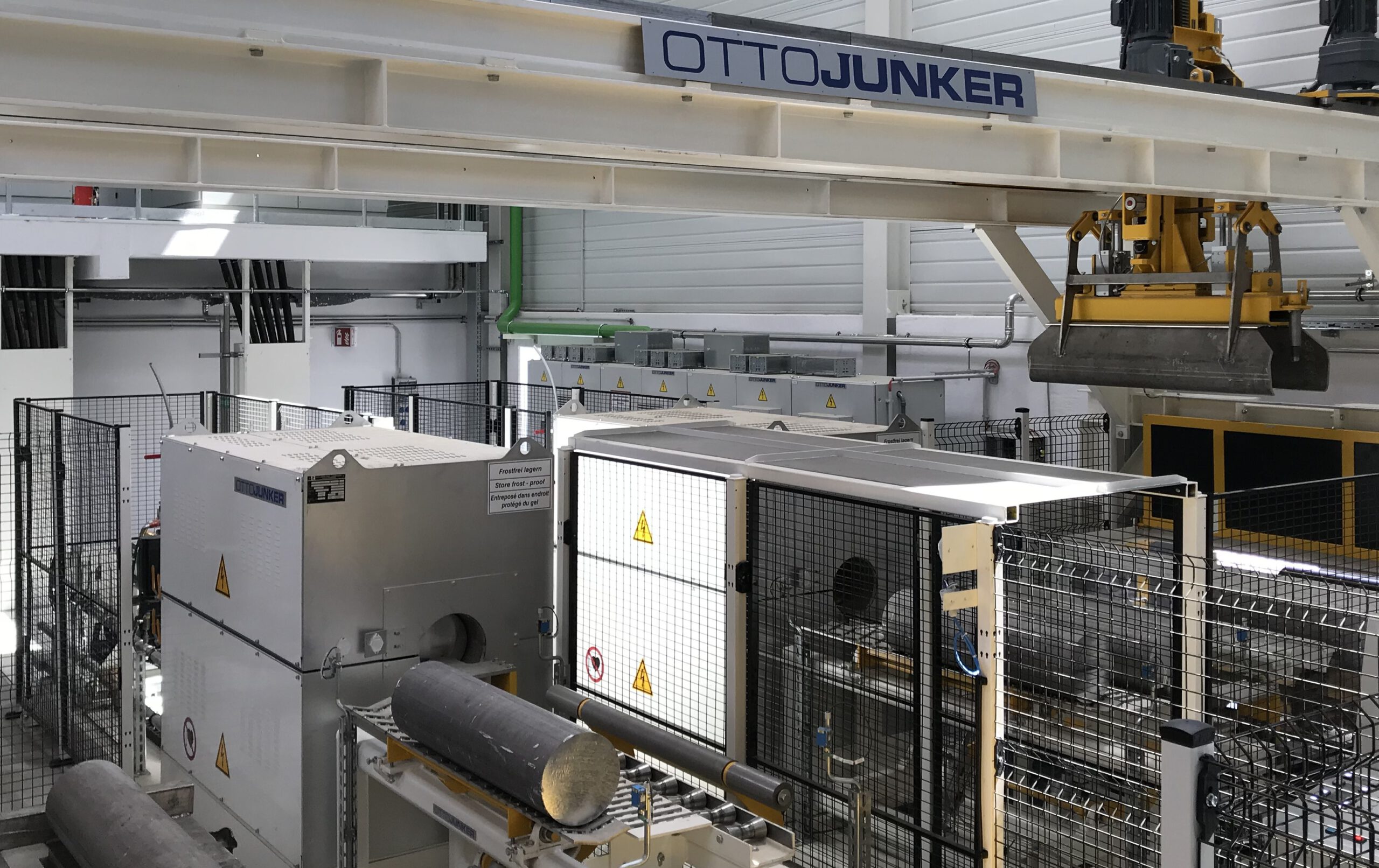
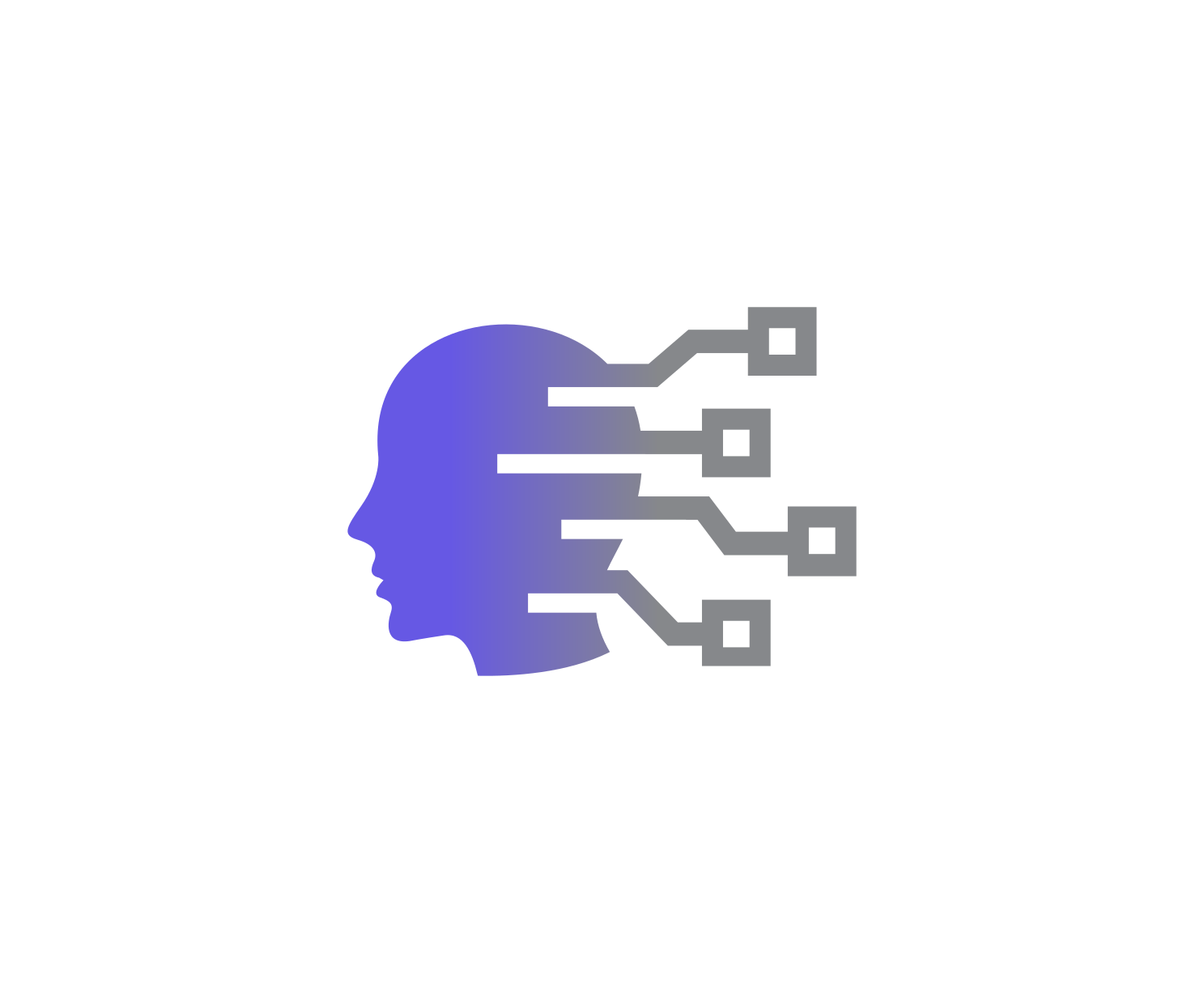